Vigorously promote internal talent cultivation! Guanyu Power invited Mr. Zou Jianmin from Jingxinzhi to give a lecture on "Use of Lean Techniques" and train the "Lean Manager" of our delivery system
2022.04.16
On April 11th, the management department of Guonyuda organized the training of "Lean Techniques application", which was lectured by The teacher Zou Jianmin from Jingxinzhi, and focused on cultivating excellent lean managers among the internal talents of Guonyuda.
After liu Qiongqing introduced the training details and process arrangement, Zou Jianmin came to the stage in the applause of everyone and started the first class of lean management training -- eliminating 10 wastes with 10 sharp tools.
More than 80 members of our delivery team participated in the study.
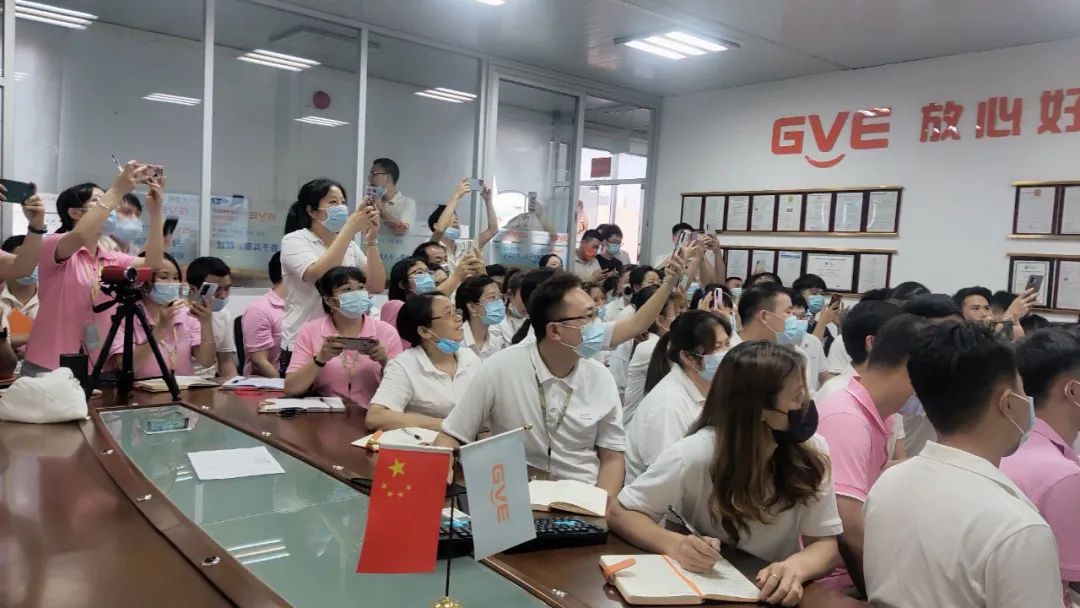
Using pictures/videos, Mr. Zou vividly explained to students the 10 key tools of lean Techniques to eliminate 10 wastes. The main contents are as follows:
First, what are the top ten wastes on the spot?
1. Creating too much waste: Producing too many things for too long
2. Waste of inventory: waste of raw materials, WIP and finished products
3, handling waste: the movement of goods, placing, processing waste
4, unqualified waste: all kinds of losses caused by incoming materials or poor production, waste of time, manpower and material resources for disposal
5. Waste of processing: waste of processing and operation unrelated to the core function of product value
6, action waste: walking, placing, large movements, etc
Waste of waiting: the waiting of materials, even if you want to promote the work can not achieve the desired state
8. Waste of management: internal friction caused by information asymmetry, weak organization and disorder caused by weakness
9, waste of staff creativity: the mechanism is not perfect, staff creativity and combat effectiveness can not play out
10, the waste of inconsistent goals: the enterprise has no strategic top-level design company has no direction, no personal goals
Two, site improvement ten sharp tools
1. Plan upward revision
2. Process flow chart
3. Assembly line calculation
4, action analysis test
5, man-machine efficiency improvement
6, transport space and time pressure
7, production abnormal call
8. Manage kanban pull
9. The root of the problem
10. Site environment change
Three, the factory eight waste
1. Waste of action
2. Waste of handling
3. Waste of waiting
4, waste of processing
5. Waste of inventory
6. Waste of repair of defective products
7. Waste of excess production
8. Waste of unused employee creativity
Only by deeply understanding the waste of production can the management make the corresponding treatment and optimization. This is the first lesson that Mr. Zou brought to the lean managers of Guanyu Da.
See you next time on Lean Techniques!
Author: Liu Qiongqing
After liu Qiongqing introduced the training details and process arrangement, Zou Jianmin came to the stage in the applause of everyone and started the first class of lean management training -- eliminating 10 wastes with 10 sharp tools.
More than 80 members of our delivery team participated in the study.
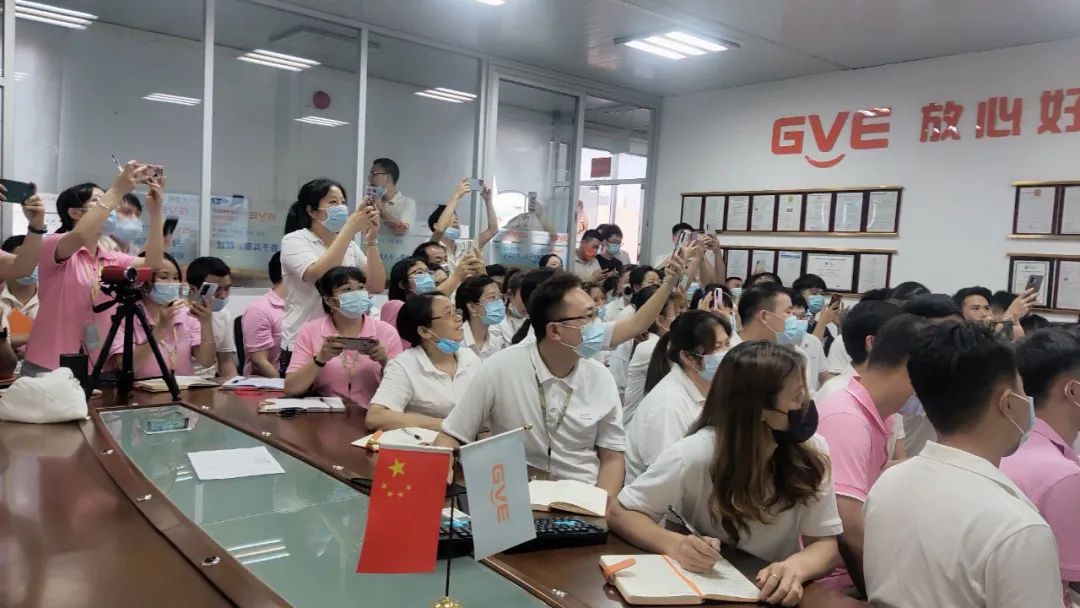
Using pictures/videos, Mr. Zou vividly explained to students the 10 key tools of lean Techniques to eliminate 10 wastes. The main contents are as follows:
First, what are the top ten wastes on the spot?
1. Creating too much waste: Producing too many things for too long
2. Waste of inventory: waste of raw materials, WIP and finished products
3, handling waste: the movement of goods, placing, processing waste
4, unqualified waste: all kinds of losses caused by incoming materials or poor production, waste of time, manpower and material resources for disposal
5. Waste of processing: waste of processing and operation unrelated to the core function of product value
6, action waste: walking, placing, large movements, etc
Waste of waiting: the waiting of materials, even if you want to promote the work can not achieve the desired state
8. Waste of management: internal friction caused by information asymmetry, weak organization and disorder caused by weakness
9, waste of staff creativity: the mechanism is not perfect, staff creativity and combat effectiveness can not play out
10, the waste of inconsistent goals: the enterprise has no strategic top-level design company has no direction, no personal goals
Two, site improvement ten sharp tools
1. Plan upward revision
2. Process flow chart
3. Assembly line calculation
4, action analysis test
5, man-machine efficiency improvement
6, transport space and time pressure
7, production abnormal call
8. Manage kanban pull
9. The root of the problem
10. Site environment change
Three, the factory eight waste
1. Waste of action
2. Waste of handling
3. Waste of waiting
4, waste of processing
5. Waste of inventory
6. Waste of repair of defective products
7. Waste of excess production
8. Waste of unused employee creativity
Only by deeply understanding the waste of production can the management make the corresponding treatment and optimization. This is the first lesson that Mr. Zou brought to the lean managers of Guanyu Da.
See you next time on Lean Techniques!
Author: Liu Qiongqing